The water well rig crawler is composed of two kinds of creeper tread and track pins. When the track pins connect the creeper tread, they form a track link. Both ends of the track plate are holes. When turning, the drive wheel engaged with an inducing tooth in the middle, so that the track can be driven regularly.
Firstly: Water well drilling rig track introduction
The water well rig crawler consists of a track shoe and a track pin. The track pin connects the track shoes to form a track link. The track shoes have holes at both ends, which are engaged with the driving wheels, and have induction teeth in the middle to regulate the tracks, and the water drilling rig prevents the tracks from falling off during the steering, and has reinforcing ribs (abbreviated as patterns) on the side in contact with the ground. Improve the robustness of the track shoe and the adhesion of the track to the ground. The water well drilling rig site also has a sprocket wheel, a roller, a drive wheel and a rail link.
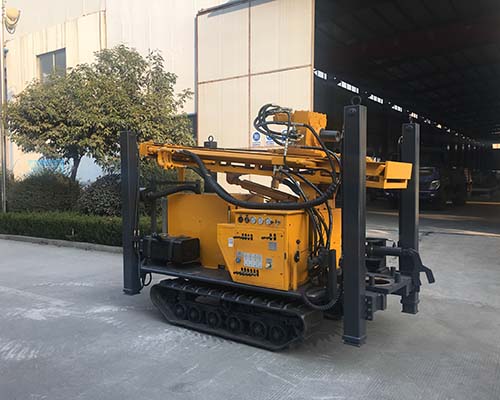
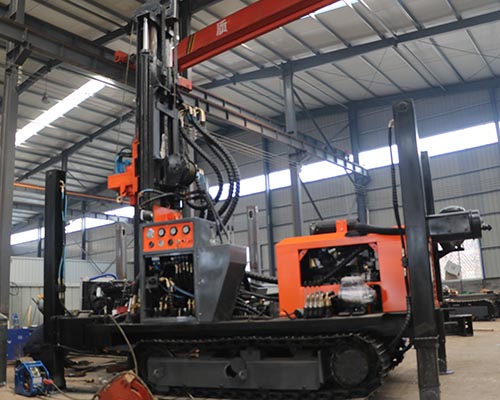
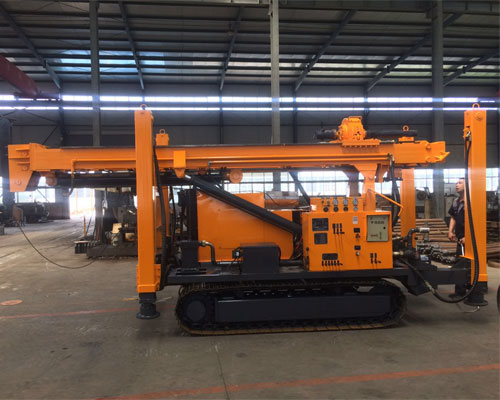
Secondly:Water well drilling track cleaning
When cleaning the rig, the sludge on the lower traveling body should be cleaned at the same time. After the operation is completed, the operator cleans the sludge on the lower traveling body while cleaning the cab, and if sludge is attached to the lower traveling body. It is not possible to check the relevant parts. Therefore, be sure to remove these sludges and inspect and maintain the lower traveling body.
Thirdly: Maintenance of water well rig track
During the construction process, the rotary drilling rig should adjust the track tension according to the soil quality to cope with the difference in soil quality of different construction sites. This can also extend the life of the machine. When the soil is soft, the soil and the rail links tend to adhere to the soil. Therefore, the track should be slightly looser to prevent the abnormal stress applied to the rail links due to the adhesion of the soil. When the construction site is spread over the pebbles, the track should be slightly looser so that the bending of the track shoes can be avoided when walking on the pebbles. When it is solid and flat, it is best to adjust the track slightly tighter. Adjusting the tension of the track: If the track is too tight, the walking speed and the running power will decrease. This not only causes a drop in work efficiency, but also causes abnormal wear due to excessive friction applied to the pin and bushing. Conversely, if the track is too loose, the track rests loosely on the drive and carrier wheels, causing more wear or damage. Moreover, when the loose track sag is too large, contact with the frame may occur and the frame may be damaged. Thus, even if the reinforced lower traveling body is not properly adjusted, an unexpected failure may occur.
Attention should be paid to reducing wear during the construction of the rotary drilling rig. The carrier roller, the roller, the drive wheel and the rail link are all wearable parts, but there are large differences depending on whether the daily inspection is carried out or not. Therefore, as long as it takes a little time to perform proper maintenance, the degree of wear can be well controlled. If the part of the carrier roller and the roller are not in operation, the roller may be worn away and the rail link may be worn. If you find a roller that cannot be operated, you must repair it immediately! In this way, other failures can be avoided. If the vehicle is repeatedly walked on the inclined ground for a long time and suddenly turns, the side of the rail link will be in contact with the side faces of the drive wheel and the guide wheel, thereby increasing the degree of wear. Therefore, walking and sudden steering in inclined areas should be avoided as much as possible. Straight line travel and large turns can effectively prevent wear.
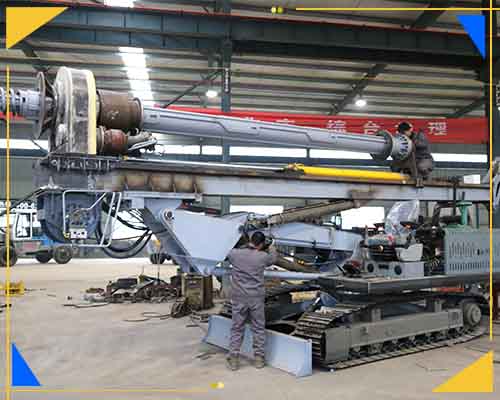
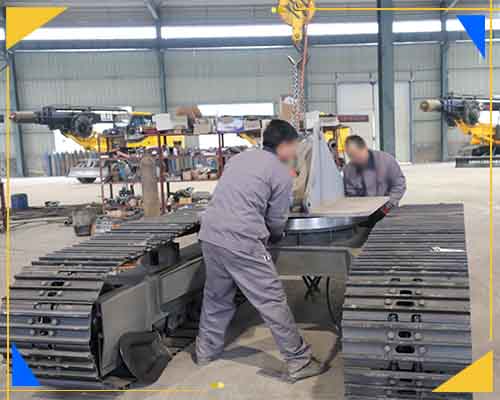
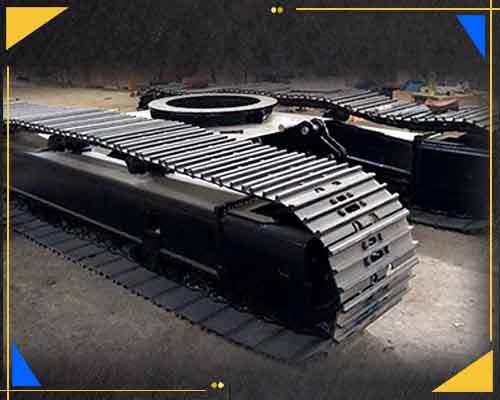
Bolts and nuts should be inspected carefully: When the machine is working for a long time, the bolts and nuts will loosen due to vibration of the machine. In particular, the bolts and nuts on the lower walking body are easily affected. If the machine continues to run with the track shoe bolts loose, a gap will be created between the bolts and the track shoes, which will cause cracks in the track shoes. Moreover, the generation of clearances may also increase the bolt holes between the track and the rail links, resulting in inability to tighten and the serious consequences of having to change the track and rail links. Therefore, bolts and nuts should be inspected regularly and tightened to reduce unnecessary costs.
The following parts should be inspected and fastened: track shoe bolts; support wheels, carrier roller mounting bolts; drive wheel mounting bolts; walking pipe bolts, etc. You should also check the parts that are not to be maintained.
In short, we must reminds the operator to pay more attention to the situation of the rotary drill track, such as loose bolts? Can the carrier roller and the roller cannot rotate? Is the carrier roller, the roller and the drive wheel leaking oil? If you ignore the above abnormal state, it will eventually lead to serious accidents. If the bolt is damaged and the related parts are damaged and the carrier roller or the roller is worn away, the maintenance cost will be greatly increased.